Owner
A costly problem of concrete construction is the schedule delay caused by the gapped delay strip. Major subcontractors are delayed from starting work in this bay see figures below.
Longer schedule delays are caused by the concrete floor gap and backshororing in the traditional delay strips (i.e., technology used for over 100 years) in concrete construction.
Further, the great conflict between cost and schedule versus quality.
PS=Ø® is the answer, to the 100 year old construction dilemma. PS=Ø® eliminates the delay gap and creates self-supporting slabs with no backshoring obstructions. Since this no gap non-delay strip is no longer on the critical path, the PS=Ø® no gap non-delay strip can be grouted/locked much later allowing for more of the concrete shrinkage to occur improving: concrete quality, while reducing contractors overhead cost by shortening the construction schedule.by months when compared to the old traditional way.
- Delays are caused by the concrete floor gap of the traditional delay strip used to minimize concrete cracking due to shrinkage
- The longer the delay strip is open the less the concrete cracks, improving concrete quality
- The gap in the concrete floor requires floor gap forming and shoring to stay in place or the forming needs be replaced for concrete casting to fill the floor gap. Backshoring must stay in place
- SCHEDULE PROBLEM – no mechanical, plumbing and electrical nor partition nor exterior façade etc. can be done in this bay until floor gap is closed by casting concrete. The delay is a minimum of 28 days. Delays of up to 90 days or more is now common.
- This costs time in the construction schedule which is money in the project overhead costs for the general contractor and all effected subcontractors
- The REVOLUTIONARY SOLUTION – PS=Ø® – no delay strip shown below
- PS=Ø® allows for the shrinkage without the delaying floor gap
- PS=Ø® can create self-supporting slabs to eliminate all backshoring
- The PS=Ø® REVOLUTIONARY SOLUTION:
- was developed by structural engineers
- mechanical coupler technology has a 50 plus year proven history
- is ICC-ES tested and approved and IBC/ACI code permitted
- is easy to install and proven in 100s of projects
- specified by the largest engineering companies
- used by the largest contractors saving months on their schedules on major projects
- Owners Options:
- Use the PS=Ø® SOLUTION for better concrete, saving time, and money
- Use the traditional gapped pour strip with the long schedule and greater project overhead costs
- Are your contractors aware of the PS=Ø® SOLUTION?
- PS=Ø® can help
- By educating your contractors on the REVOLUTIONARY PS=Ø® SOLUTION
- By offering you a list to knowledgeable, experienced contactors
- PS=Ø® can help
Traditional Concrete Construction
All concrete shrinks
- Elevated concrete construction traditionally has a floor gapped delay strip to reduce shrinkage cracking
- The delay strips improve concrete quality – long delay is better quality concrete
- The delay strips delays the subcontractors especially mechanical, plumbing and electrical due to the floor gap of the traditional delay strip and all the forming and shoring that remains in place
Traditional DELAY Strip Construction
PS=Ø® Revolutionizing The Construction Industry
- PS=Ø® Revolutionizing the Construction of elevated concrete construction eliminates the traditionally floor gap delay strip to reduce shrinkage cracking
- The PS=Ø® No delay strips further improving concrete quality by allowing even longer open times for even better quality concrete
- The PS=Ø® No floor gap, No delay strip allows the subcontractors especially mechanical, plumbing and electrical to start months earlier, than the traditional method
- PS=Ø® REVOLUTIONARY SOLUTION eliminates traditionally required forming and backshoring simplifying and speeding construction for subcontractors that follow
- PS=Ø® can improve concrete quality by grouting much later 120 days or more without delaying the project schedule
PS=Ø® Revolutionizing Concrete Construction
Items Affected by Using PS=Ø®
- 1. Budget and Cost Control
- PS=Ø® provides for months faster construction saving months of overhead cost.
- Project Budget: Owners are highly concerned about staying within budget, as construction projects can be very expensive. They expect contractors and project managers to control costs and minimize overruns.
- Cost Transparency: Owners prefer to have a clear understanding of how funds are being spent, including material costs, labor, and any potential changes that may increase expenses.
- 2. Timeline and Schedule
- On-time Completion: Owners expect the project to be completed on schedule, as delays can result in financial loss or disruptions to business operations.
- PS=Ø® provides for months faster construction.
- Milestones and Progress: Regular updates on project milestones help owners gauge whether the project is on track and allow for adjustments if necessary.
- 3. Risk Management
- Identifying Risks: Owners want potential risks identified early on, whether related to materials, environmental issues, or unforeseen site conditions.
- PS=Ø® provides for safer construction with the gapless no-delay strip.
- Mitigating Issues: They are concerned with how risks are mitigated and expect contractors to have contingency plans for handling delays, cost overruns, or safety hazards.
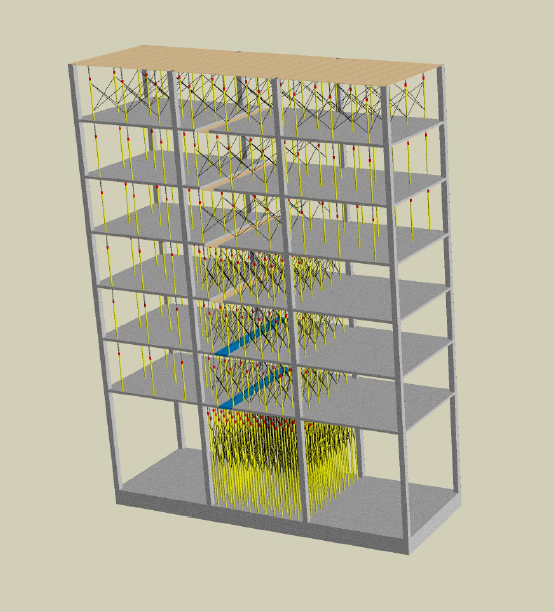
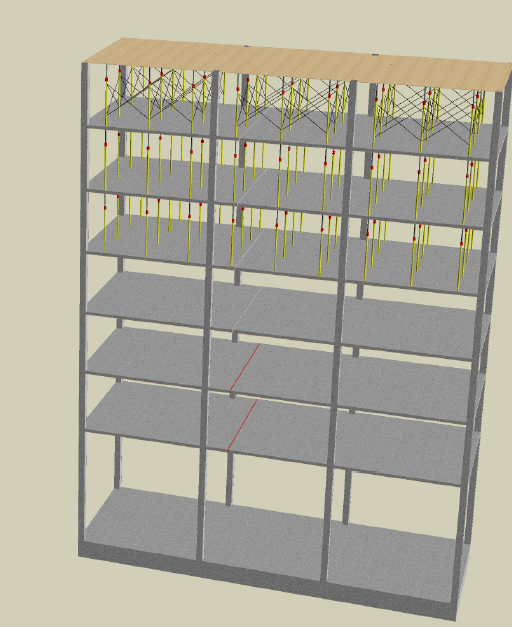
Items Unaffected by Using PS=Ø®
3. Quality of Workmanship
- Materials and Standards: The quality of materials and workmanship is critical, as the owner wants to ensure that the final product will be durable, functional, and aesthetically pleasing.
- Compliance with Codes: The project must meet all applicable building codes, safety standards,
- 4. Communication and Transparency
- Clear Communication: Open lines of communication between the owner, contractors, and project managers are essential for the smooth execution of the project.
- Regular Updates: Owners appreciate regular updates on project progress, challenges, and changes. This includes progress reports, change orders, and site inspections.
- 5. Change Orders and Flexibility
- Managing Changes: Construction projects often involve changes due to design modifications or unforeseen issues. Owners expect these to be handled efficiently and without significant cost or time impact.
- Flexibility: Owners value flexibility in the process, whether it involves minor design tweaks or major scope changes.
- 6. Sustainability and Environmental Concerns
- Eco-friendly Practices: Owners may prioritize sustainable construction methods, energy efficiency, and the use of environmentally friendly materials, depending on their personal or corporate values.
- Compliance with Environmental Regulations: Projects need to meet environmental standards to avoid penalties and ensure the building is sustainable for future use.
- 7. Post-Construction Supp