Concrete Contractor
by allowing early starts for major subcontractors, it is so Simple.
A costly problem of concrete construction is the schedule delay caused by the gapped delay strip. Major subcontractors are delayed from starting work in this bay see figures below.
Win more projects by helping improve your general contractors schedule by using the PS=Ø® answer. PS=Ø® staff can help.
OR lose projects by not including PS=Ø® Revolutionizing Technology
Longer schedule delays are caused by the concrete floor gap in the traditional delay strips (i.e., technology used for over 100 years) in concrete construction.
Further, the great conflict between cost and schedule versus quality.
PS=Ø® is the answer, to the 100 year old construction dilemma. PS=Ø® eliminates the delay gap and creates self-supporting slabs with no backshoring obstructions. Since this no gap non-delay strip is no longer on the critical path, the PS=Ø® no gap non-delay strip can be grouted/locked much later allowing for more of the concrete shrinkage to occur improving: concrete quality, while reducing contractors overhead cost by shortening the construction schedule.by months when compared to the old traditional way.
Long schedules are caused by the concrete floor gap in the traditional delay strips (i.e., technology used for over 100 years) in concrete construction.
- Delays are caused by the concrete floor gap of the traditional delay strip used to minimize concrete cracking due to shrinkage
- The longer the delay strip is open the less the concrete cracks, improving concrete quality
- The gap in the concrete floor requires floor gap forming and shoring to stay in place or the forming needs be replaced for concrete casting to fill the floor gap. Backshoring must stay in place
- SCHEDULE PROBLEM – no mechanical, plumbing and electrical nor partition nor exterior façade etc. can be done in this bay until floor gap is closed by casting concrete. The delay is a minimum of 28 days. Delays of up to 90 days or more is now common.
- This costs time in the construction schedule which is money in the project overhead costs for the general contractor and all effected subcontractors
- The REVOLUTIONARY SOLUTION – PS=Ø® – no delay strip shown below
- PS=Ø® allows for the shrinkage without the delaying floor gap
- PS=Ø® can create self-supporting slabs to eliminate all backshoring
- The PS=Ø® REVOLUTIONARY SOLUTION:
- was developed by structural engineers
- mechanical coupler technology has a 50 plus year proven history
- is ICC-ES tested and approved and IBC/ACI code permitted
- is easy to install and proven in 100s of projects
- specified by the largest engineering companies
- used by the largest contractors saving months on their schedules on major projects
- Concrete Contractors Options:
- Use the PS=Ø® SOLUTION for better concrete, saving time, and money making the General Contractor’s scheduling easier and faster
- Labor savings as the concrete contractor you have no backshoring
- No backshoring
- estimate is 1-man-hour per shore post plus crane time
- No backshoring
- Labor savings as the concrete contractor you have no backshoring
- Use the traditional gapped pour strip
- continuing the long schedule
- and greater project overhead costs
- make it difficult for your general contractor meet the project scheduleIS
- Use the PS=Ø® SOLUTION for better concrete, saving time, and money making the General Contractor’s scheduling easier and faster
- Is your general contractor aware of the PS=Ø® SOLUTION?
- PS=Ø® can help
- By educating your general contractor on the REVOLUTIONARY PS=Ø® SOLUTION and the general contractor’s advantage using the PS=Ø® system. Particularly how it will ease his schedule issues
- PS=Ø® can help
Traditional Concrete Construction
All concrete shrinks
- Elevated concrete construction traditionally has a floor gapped delay strip to reduce shrinkage cracking
- The delay strips improve concrete quality – long delay is better quality concrete
- The delay strips delays the subcontractors especially mechanical, plumbing and electrical due to the floor gap of the traditional delay strip and all the forming and shoring that remains in place
Traditional DELAY Strip Construction
PS=Ø® Revolutionizing The Construction Industry
- PS=Ø® Revolutionizing the Construction of elevated concrete construction eliminates the traditionally floor gap delay strip to reduce shrinkage cracking
- The PS=Ø® No delay strips further improving concrete quality by allowing even longer open times for even better quality concrete
- The PS=Ø® No floor gap, No delay strip allows the subcontractors especially mechanical, plumbing and electrical to start months earlier, than the traditional method
- PS=Ø® REVOLUTIONARY SOLUTION eliminates traditionally required forming and backshoring simplifying and speeding construction for subcontractors that follow
- PS=Ø® can improve concrete quality by grouting much later 120 days or more without delaying the project schedule
PS=Ø® Revolutionizing Concrete Construction
Items Affected by Using PS=Ø®
- In the concrete building construction process, the concrete contractor plays a specialized role, focusing on the preparation, pouring, and finishing of concrete. Their responsibilities are crucial for the structural integrity, durability, and overall success of the project. Here are the key factors that are important to the concrete contractor:
- 1. Accurate Planning and Preparation
- Site Preparation: Ensuring the site is properly prepared before pouring concrete is critical. This includes grading, compacting the subgrade, and setting up the formwork.
- Formwork: Correct installation of formwork (the molds that shape the concrete) is essential to achieving the required dimensions and structural integrity. Poor formwork can lead to defects in the final product.
- PS=0 no gap no delay strip eliminates the leave behind forming required for the tradition gapped delay strip.
- Shoring: Backshoring is most expensive whereas reshoring is less costly and most desired if possible. To eliminate expensive backshoring concrete slabs must be self-supporting. Most engineered plan expensive is required. These shoring conditions are fully explained in ACI 347.
- PS=0 can develop self-supporting slabs with a no gap no delay strip, thus eliminating the leave behind traditional gapped delay forming and expensive backshoring. This reduces site labor and shortens the construction schedule that reduces overhead cost.
- Reinforcement: The concrete contractor must ensure that steel reinforcement (rebar or mesh) is correctly placed, as it strengthens the concrete and helps resist cracking and structural failure.
- 2. Safety on Site
- Worker Safety: Concrete construction involves heavy equipment, hazardous materials, and manual labor. The contractor must implement strict safety protocols to protect workers, including proper personal protective equipment (PPE), training, and safety procedures.
- PS=0 can develop self-supporting slabs with a no gap no delay strip, that is obviously safer than the traditional gapped delay strip. Further less shoring moving and no moving of forming for the traditional gapped delay strip is surely safer.
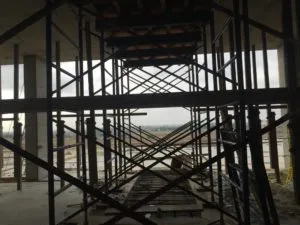
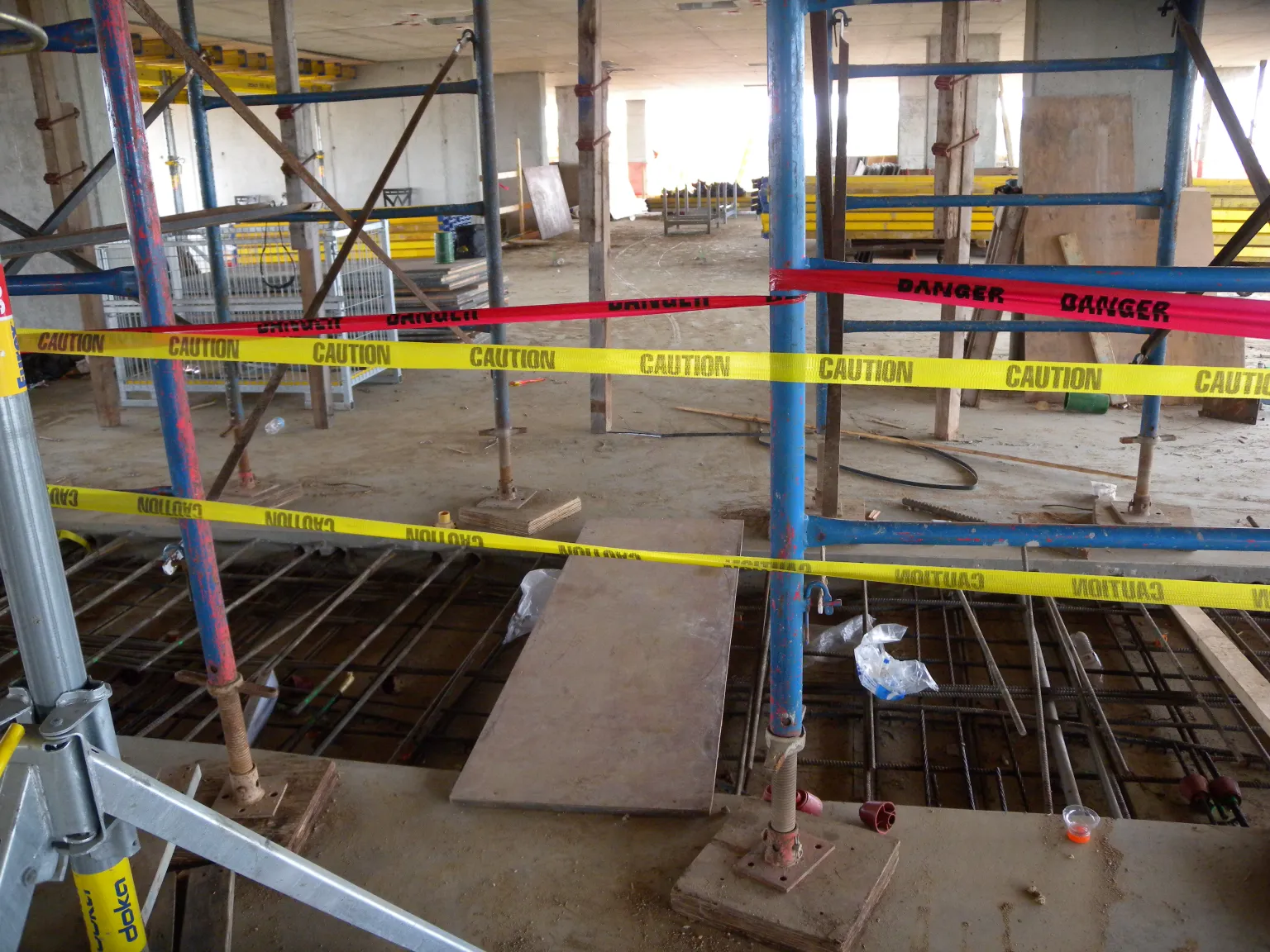
Top and bottom of PS=Ø® no gap no delay strip no delayed forming
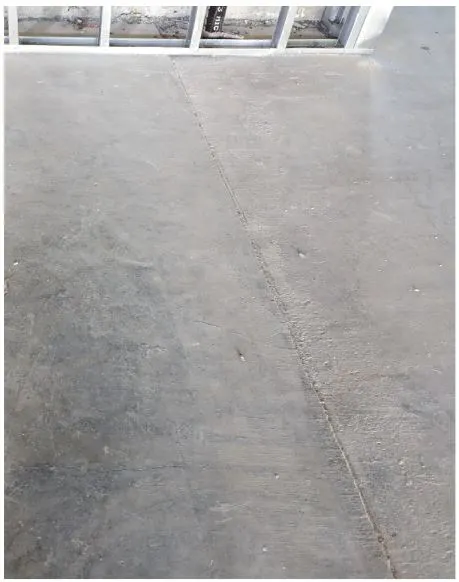
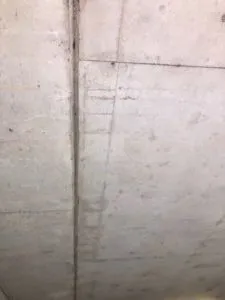
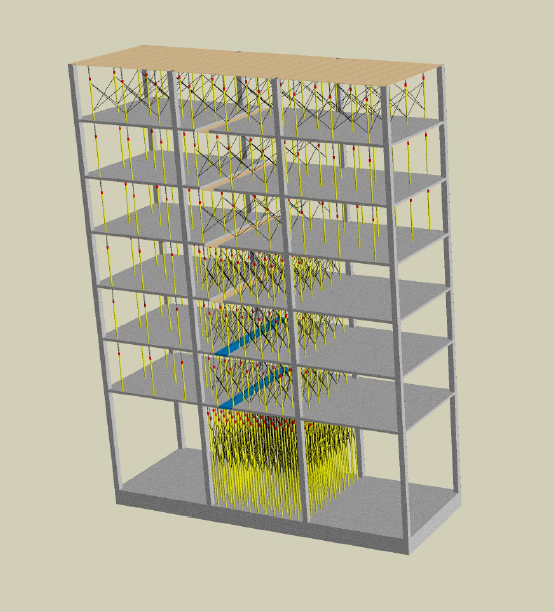
Forming and backshoring required. Longer delay strips for better concrete quality result in longer construction delays.
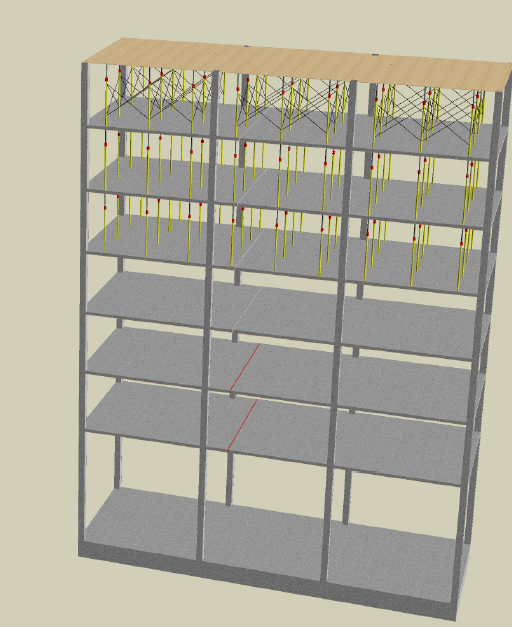
Items Unaffected by Using PS=Ø®
- 3. Concrete Mix Quality
- Mix Design: Selecting the appropriate concrete mix is one of the contractor’s top priorities. The mix must be suited to the building’s load-bearing requirements, environmental conditions, and durability needs.
- Material Quality: Ensuring the quality of raw materials—such as cement, aggregates, and water—is crucial. Poor-quality materials can lead to weak or defective concrete.
- Additives and Admixtures: The concrete contractor must choose the right additives (e.g., water reducers, accelerators, or retarders) depending on the required properties, such as strength, curing time, or resistance to temperature variations.
- 4. Pouring and Placement
- Timely Placement: Concrete must be poured and placed within a specific time frame after mixing to ensure its workability and strength. Delays or improper handling can lead to weakened concrete.
- Proper Compaction: Vibrating or compacting the concrete during placement is important to remove air pockets (voids) and ensure uniform density and strength.
- Leveling and Screeding: Ensuring the concrete is properly leveled and screeded (flattened to the correct height) is important to achieve the desired surface finish and avoid defects like dips or uneven surfaces.
- 5. Curing Process
- Proper Curing: Curing the concrete is critical to developing its strength and durability. The contractor must ensure proper curing methods (e.g., keeping the surface moist, using curing compounds) are followed for the recommended duration.
- Avoiding Premature Drying: Concrete that dries too quickly can develop cracks or shrinkage, so contractors need to monitor temperature, wind, and humidity conditions during and after the pour.
- 6. Weather Conditions
- Temperature and Climate Control: Weather has a significant impact on concrete work. In hot conditions, the concrete can dry too quickly, leading to cracking, while in cold conditions, the water in the concrete can freeze, affecting its strength. The contractor must take measures to control the environment, such as using curing blankets or accelerators.
- Timing the Pour: Contractors often need to plan concrete pours around the weather forecast to avoid rain, extreme heat, or freezing conditions, which can compromise the quality of the finished concrete.
- 7. Communication and Coordination
- Worker Safety: Concrete construction involves heavy equipment, hazardous materials, and manual labor. The contractor must implement strict safety protocols to protect workers, including proper personal protective equipment (PPE), training, and safety procedures.
- Hazardous Material Handling: Proper handling and disposal of concrete-related materials, such as cement dust or chemical admixtures, is necessary to ensure environmental compliance and worker safety.
- 8. Project Timeline and Scheduling
- Timely Execution: Concrete contractors must adhere to the overall project timeline, ensuring that their work is completed within the required windows. Delays can have cascading effects on other trades and the project schedule.
- Efficient Use of Resources: The contractor must manage labor, materials, and equipment effectively to ensure that the concrete is mixed, delivered, and placed on time without wasting resources.
- 9. Quality Control and Inspections
- Testing and Inspection: Quality control is essential in concrete work. The contractor is responsible for ensuring that the concrete meets the project’s specified strength requirements, typically through slump tests, compression tests, and inspection of the formwork and reinforcement.
- Surface Finish and Aesthetic: In some cases, the concrete finish is important for both structural and aesthetic reasons. Contractors must ensure a high-quality finish (e.g., smooth or textured surfaces) depending on the project requirements.
- 10. Cost Management
- Controlling Material Costs: Concrete contractors must manage the cost of raw materials and ensure that they are not over-ordered or wasted during the project.
- Labor Efficiency: Keeping labor costs under control by optimizing work schedules and minimizing overtime is also a key focus for the concrete contractor.
- Avoiding Rework: Mistakes in concrete work can be expensive to fix, so the contractor focuses on precision during each phase to avoid costly rework or demolition of defective areas.
- 11. Change Order Management
- Managing Design Changes: Concrete contractors often face changes to the original design or scope, such as adjustments to slab thickness, column placement, or reinforcement details. Handling these changes efficiently and integrating them into the work without disrupting the schedule is important.
- Cost Adjustments: Contractors must ensure that change orders are properly documented and compensated, especially when they involve additional materials, labor, or time.
- 12. Post-Construction and Maintenance
- Defect Management: After the concrete is placed, the contractor may need to address any surface defects, such as cracks, spalling, or scaling. They must ensure that these issues are identified and resolved during the final inspection phase.
- Long-Term Durability: Ensuring the concrete’s long-term durability, especially in terms of water resistance, freeze-thaw cycles, and exposure t“`o chemicals, is critical to avoid future issues or callbacks.
- 13. Environmental Considerations
- Waste Management: Proper disposal of excess concrete and other construction debris is necessary to comply with environmental regulations.
- Sustainability: Some projects may require the contractor to implement eco-friendly practices, such as using recycled materials, low-carbon concrete mixes, or other sustainable techniques to reduce the environmental impact.
- In summary, the concrete contractor is focused on delivering high-quality concrete work that meets structural and aesthetic specifications while ensuring safety, efficiency, and compliance with project timelines and budgets. The PS=Ø® no gap no delay strip is obviously safer and less costly with no backshoring and no forming left behind to cast the gap delay strip concrete is substantially less costly. Further, the PS=Ø® only requires a small crew to grout the PS=Ø® and joint. Managing variables such as weather, material quality, and communication with other trades is critical to their success in the construction process.