Structural Engineer
PS=Ø® Revolutionizing The Construction Industry
by allowing early starts for major subcontractors and it is so Simple.
A costly problem of concrete construction is the schedule delay caused by the gapped delay strip. Major subcontractors are delayed from starting work in this bay see figures below.
As a the Engineer of Record (EOR) you can specify the PS=Ø® System for better quality concrete and shorten your Owner’s construction schedule saving contractor overhead cost. (PS=Ø® has lists of general and concrete contactors throughout the US who have achieved these concrete quality improvements and cost saving.)
At a minimum you could always specify the PS=Ø® System and the traditional gapped delay strip as an alternate, which will challenge you, as the general and concrete contractors will often demand closing the gap early, reducing quality, to meet the general contractor’s schedule. This is the challenge and dilemma of traditional gapped delay strip in concrete construction.
Longer schedule delays are caused by the concrete floor gap in the traditional delay strips (i.e., technology used for over 100 years) in concrete construction.
Further, the great conflict between cost and schedule versus quality.
PS=Ø® is the answer, to the 100 year old construction dilemma. PS=Ø® eliminates the delay gap and creates self-supporting slabs with no backshoring obstructions. Since this no gap non-delay strip is no longer on the critical path, the PS=Ø® no gap non-delay strip can be grouted/locked much later allowing for more of the concrete shrinkage to occur improving: concrete quality, while reducing contractors overhead cost by shortening the construction schedule.by months when compared to the old traditional way.
- Delays are caused by the concrete floor gap of the traditional delay strip used to minimize concrete cracking due to shrinkage
- The longer the delay strip is open the less the concrete cracks, improving concrete quality
- The gap in the concrete floor requires floor gap forming and shoring to stay in place or the forming needs be replaced for concrete casting to fill the floor gap. Backshoring must stay in place
- SCHEDULE PROBLEM – no mechanical, plumbing and electrical nor partition nor exterior façade etc. can be done in this bay until floor gap is closed by casting concrete. The delay is a minimum of 28 days. Delays of up to 90 days or more is now common.
- This costs time in the construction schedule which is money in the project overhead costs for the general contractor and all effected subcontractors
- The REVOLUTIONARY SOLUTION – PS=Ø® – no delay strip shown below
- PS=Ø® allows for the shrinkage without the delaying floor gap
- PS=Ø® can create self-supporting slabs to eliminate all backshoring
- The PS=Ø® REVOLUTIONARY SOLUTION:
- was developed by structural engineers
- mechanical coupler technology has a 50 plus year proven history
- is ICC-ES tested and approved and IBC/ACI code permitted
- is easy to install and proven in 100s of projects
- specified by the largest engineering companies
- used by the largest contractors saving months on their schedules on major projects
- Owners Options:
- Use the PS=Ø® SOLUTION for better concrete, saving time, and money
- Use the traditional gapped pour strip with the long schedule and greater project overhead costs
- Are your contractors aware of the PS=Ø® SOLUTION?
- PS=Ø® can help
- By educating your contractors on the REVOLUTIONARY PS=Ø® SOLUTION
- By offering you a list to knowledgeable, experienced contactors
- PS=Ø® can help
Traditional Concrete Construction
All concrete shrinks
- Elevated concrete construction traditionally has a floor gapped delay strip to reduce shrinkage cracking
- The delay strips improve concrete quality – long delay is better quality concrete
- The delay strips delays the subcontractors especially mechanical, plumbing and electrical due to the floor gap of the traditional delay strip and all the forming and shoring that remains in place
Concrete Floor Gap in the Traditional DELAY Strip Construction
PS=Ø® Revolutionizing The Construction Industry
- PS=Ø® Revolutionizing the Construction of elevated concrete construction eliminates the traditionally floor gap delay strip to reduce shrinkage cracking
- The PS=Ø® No delay strips further improving concrete quality by allowing even longer open times for even better quality concrete
- The PS=Ø® No floor gap, No delay strip allows the subcontractors especially mechanical, plumbing and electrical to start months earlier, than the traditional method
- PS=Ø® REVOLUTIONARY SOLUTION eliminates traditionally required forming and backshoring simplifying and speeding construction for subcontractors that follow
- PS=Ø® can improve concrete quality by grouting much later 120 days or more without delaying the project schedule
PS=Ø® Revolutionizing Concrete Construction
Items Affected by Using PS=Ø®
- In the concrete building construction process, the structural engineer plays a critical role in ensuring that the structure is safe, stable, and able to withstand various forces. Their focus is on designing, analyzing, and supervising the construction to ensure the structural integrity of the building. Key factors important to the structural engineer include:
- 1. Adherence to Codes and Standards
- Building Codes: Structural engineers ensure that the building design complies with local, national, and international building codes, including seismic codes, fire safety standards, and wind resistance requirements.
- Design Standards: They use industry standards (e.g., ACI, ASCE, Eurocode) to design and analyze concrete structures, ensuring the building meets safety and performance criteria
- PS=خis code permitted and the engineer can meet all integrity provisions of ACI just like the traditional delay strip. PS=0 also provide the opportunity to for shrinkage to occur over much longer times as this no gap no d elay strip is no longer on the construction critical path.
- 2. Structural Integrity and Safety
- Load-Bearing Capacity: The structural engineer is responsible for ensuring the building can safely bear the loads it is subjected to, including live loads (people, furniture, etc.), dead loads (the building’s own weight), and environmental loads (wind, earthquakes, etc.).
- The PS=Ø® provide ACI code integrity and is better safety is proved by the no gap no delay strip.
- Stability: The structure must remain stable under all conditions, resisting forces like gravity, wind, and seismic activity without collapsing or excessive movement.
- Stability: The structure must remain stable under all conditions, resisting forces like gravity, wind, and seismic activity without collapsing or excessive movement.
Traditional Gapped Delay Strip PS=Ø® No Gap Non-Delay Strip
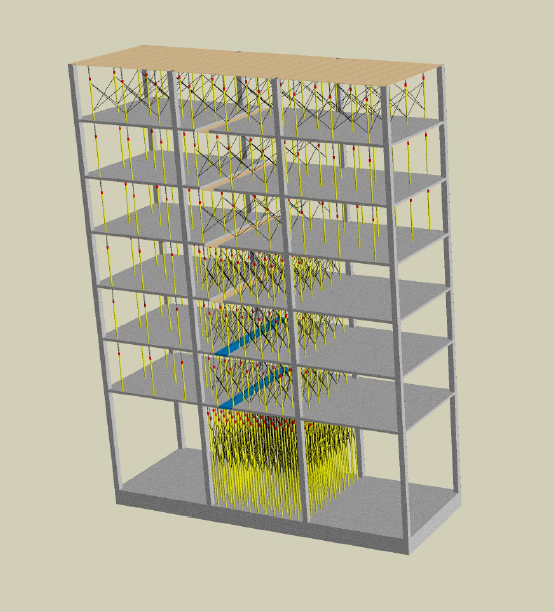
Backshored
Forming and backshoring are necessary. Using longer delay strips to enhance concrete quality leads to extended construction timelines.
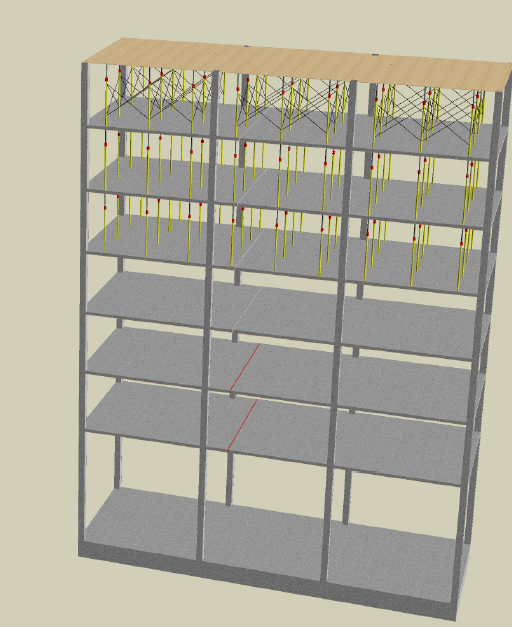
Reshored only
PS=Ø® pour strip creates self-supporting slabs; thus only reshoring is required. No cost for backshoring and floors are available months soon for advancing other construction trades.
Items Unaffected by Using PS=0
- 3. Concrete Strength and Material Properties
- Specified Strength: The structural engineer specifies the required compressive strength of the concrete based on the building’s load requirements. Ensuring that the mix design meets this strength specification is crucial for the overall safety of the structure.
- Durability: The concrete must be durable enough to withstand environmental conditions such as moisture, temperature changes, freeze-thaw cycles, and chemical exposure over time.
- Reinforcement: Engineers design the placement and amount of steel reinforcement (rebar) in the concrete to handle tensile forces, as concrete is weak in tension but strong in compression.
- 4. Structural Design and Analysis
- Load Distribution: Structural engineers focus on how loads are distributed through the concrete structure, ensuring that the foundation, columns, beams, and slabs are properly designed to transfer these loads.
- Deflection and Movement: Controlling deflection (bending) and limiting movement under load is important to prevent damage to the building or discomfort to occupants. Engineers design for both serviceability (crack control, vibration) and strength.
- Seismic and Wind Design: In areas prone to earthquakes or strong winds, engineers must design the concrete structure to absorb and dissipate energy from these forces without failure.
- 5. Foundation Design
- Soil and Ground Conditions: The foundation design is critical to the overall stability of the structure. Structural engineers analyze soil conditions to determine the type of foundation (e.g., slab, deep foundations, or piles) that will best support the concrete building.
- Settlement and Bearing Capacity: The foundation must be designed to prevent excessive settlement, ensuring that the soil can support the loads without causing structural issues.
- 6. Coordination with the Architect and Other Disciplines
- Design Integration: Structural engineers must coordinate with architects to ensure that the structural design aligns with the building’s architectural vision without compromising safety. They also work with mechanical, electrical, and plumbing (MEP) engineers to integrate systems without interfering with the structure.
- Load Paths and Openings: Openings for doors, windows, and mechanical systems need to be accounted for in the structural design. The engineer ensures that these do not weaken the structural members or disrupt load paths.
- 7. Construction Supervision and Quality Control
- Construction Monitoring: Structural engineers often supervise the construction process to ensure that the concrete is placed, reinforced, and cured according to design specifications. They inspect formwork, reinforcement placement, and concrete quality.
- Quality Assurance: Ensuring that the concrete used meets design strength, mix quality, and curing requirements is a priority. They may require on-site tests, such as slump tests and compression tests, to verify the concrete’s quality.
- 8. Reinforcement Detailing
- Rebar Placement: Structural engineers carefully design the layout of reinforcing steel within the concrete to handle tensile forces and prevent cracking. Incorrect placement can lead to weak points and structural deficiencies.
- Anchorage and Lap Splices: Engineers specify how reinforcement bars are anchored and spliced (overlapping to create continuous strength) to ensure the concrete structure can resist loads effectively.
- 9. Construction Tolerances
- Dimensional Accuracy: The structural engineer sets allowable tolerances for concrete placement, formwork, and reinforcement to ensure that the finished structure meets design specifications. Deviations beyond the tolerances can impact the performance and safety of the building.
- Concrete Cover: Ensuring proper concrete cover over reinforcement is essential to protect the steel from corrosion and ensure fire resistance.
- 10. Creep, Shrinkage, and Temperature Effects
- Long-Term Effects: Structural engineers design the concrete to account for long-term behaviors such as creep (gradual deformation under load) and shrinkage (reduction in volume due to water loss), which can affect the building’s performance over time.
- Thermal Effects: Concrete can expand and contract with temperature changes, so the engineer must design for thermal movement to prevent cracking or structural issues.
- 11. Change Order Management
- Design Modifications: During construction, changes in the design or unforeseen site conditions may arise. Structural engineers are responsible for assessing the impact of these changes on the structure and making necessary adjustments.
- Impact on Structural Integrity: When changes are made, engineers must ensure they do not compromise the safety or stability of the building, especially in critical areas like load-bearing elements.
- 12. Sustainability and Environmental Considerations
- Material Efficiency: Structural engineers often focus on using materials efficiently to reduce waste and optimize the amount of concrete and steel needed. This reduces the environmental impact and lowers costs.
- Sustainable Practices: Engineers may consider the use of sustainable materials, such as recycled aggregates or low-carbon concrete, to meet the growing demand for environmentally friendly building practices.
- 13. Post-Construction and Maintenance Planning
- Structural Monitoring: After the building is completed, the structural engineer may be involved in monitoring the building’s performance, including identifying potential issues like cracking, deflection, or settlement.
- Maintenance Plans: Engineers provide recommendations for long-term maintenance, such as addressing potential corrosion of reinforcement or periodic inspections of structural components.
- 14. Failure Analysis and Mitigation
- Designing for Redundancy: Structural engineers build redundancy into the design so that if one element fails, the load can be redistributed to prevent catastrophic failure.
- Risk Mitigation: Engineers analyze potential failure modes, such as cracking, buckling, or collapse, and incorporate safety measures like increased reinforcement, expansion joints, or stronger materials.
- In summary, the structural engineer focuses on ensuring the safety, durability, and performance of the concrete structure. Their work revolves around load-bearing capacity, structural analysis, reinforcement detailing, code compliance, and coordinating with other professionals. Structural engineers ensure the concrete building will stand the test of time, withstand environmental forces, and function safely and efficiently
- throughout its lifespan.